生產(chǎn)端子用銅帶的工藝流程涉及多個步驟,主要包括原材料準備、軋制、退火、清洗、表面處理、裁剪和質(zhì)量檢測等環(huán)節(jié)。以下是詳細的端子用銅帶生產(chǎn)工藝流程:
1. 原材料準備
原材料選擇:根據(jù)端子銅帶的具體要求,選擇優(yōu)質(zhì)的銅原料,通常為銅坯或銅線坯。
銅合金的準備:如果需要鍍層或合金材料,可以選擇鍍銀、鍍鋅、鍍錫等不同類型的銅合金。
清潔處理:在生產(chǎn)前,清除原材料表面的雜質(zhì)、氧化物和油污,確保銅材表面干凈。
2. 熱軋或冷軋
熱軋:將銅坯加熱到一定溫度后進行軋制,使其塑性提高并降低硬度。熱軋后的銅材可以初步成形為較厚的銅帶。
冷軋:在常溫下通過軋機將銅材進一步壓延,減少厚度,提高其強度、延展性和表面光潔度。冷軋后的銅帶通常具有較高的精度和質(zhì)量。
3. 中間退火
目的:退火的目的是去除軋制過程中銅材產(chǎn)生的內(nèi)部應力,恢復材料的柔韌性,改善后續(xù)加工性能。
退火工藝:將軋制后的銅帶加熱到一定溫度,然后緩慢冷卻。這個過程可以軟化材料,使其具備更好的延展性。
4. 酸洗與清洗
酸洗:退火后的銅帶表面可能會產(chǎn)生氧化物和雜質(zhì),因此需要通過酸洗去除。通常使用稀硫酸或其他化學試劑。
清洗:酸洗后需要使用純凈水將銅帶徹底清洗干凈,以防止酸液殘留,影響后續(xù)的鍍層處理和產(chǎn)品質(zhì)量。
5. 表面處理
電鍍處理:根據(jù)客戶要求進行表面鍍層處理,比如鍍錫、鍍鎳、鍍銀等,以提升銅帶的導電性、耐腐蝕性和抗氧化能力。
鈍化處理:有時為了增強銅帶的耐腐蝕性,還可能進行鈍化處理,進一步保護表面。
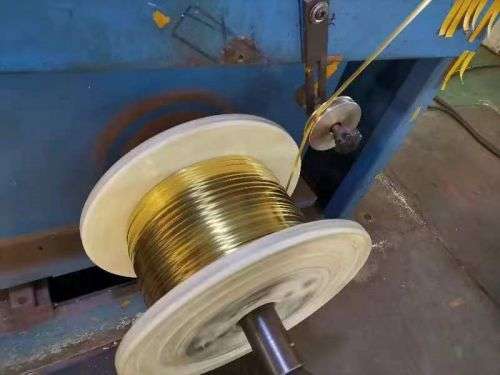
6. 精密裁剪
裁剪尺寸:將生產(chǎn)的銅帶根據(jù)端子需求裁剪成適合的尺寸,寬度和厚度根據(jù)客戶規(guī)格進行精密裁切。
定尺處理:確保銅帶尺寸符合精度要求,如寬厚比,平整度,邊緣光滑等方面,特別是對于高精度應用的端子用銅帶。
7. 成品檢測
尺寸檢測:使用專業(yè)檢測設備對銅帶的厚度、寬度進行精密測量,確保尺寸的精度。
表面質(zhì)量檢查:檢查銅帶表面是否有缺陷,如劃痕、氧化斑點或雜質(zhì),確保表面光潔度。
性能測試:對銅帶的導電性、抗拉強度、延展性等進行檢測,確保符合端子的功能需求。
顯微鏡檢測:通過高精度顯微鏡檢查銅帶的斷面質(zhì)量,確保其晶粒組織均勻,避免內(nèi)部瑕疵。
8. 包裝和出貨
卷繞成卷:將符合標準的銅帶卷繞成一定長度的銅卷,便于運輸和使用。
包裝:使用防潮、防塵包裝材料對銅帶進行密封包裝,防止運輸過程中受到污染和損壞。
出貨:完成包裝后,將產(chǎn)品根據(jù)客戶的需求發(fā)送至指定地點。
關(guān)鍵點注意:
尺寸控制:冷軋和裁剪過程中必須嚴格控制銅帶的寬厚比,尤其是在生產(chǎn)高精度銅帶時,對設備和操作員的要求很高。
表面處理:鍍層工藝和酸洗處理必須精確到位,否則會影響銅帶的導電性和耐腐蝕性。
安全生產(chǎn):高溫軋制、退火過程和酸洗過程需要工人特別注意安全防護,避免灼傷或化學品傷害。
通過這一系列精密的工藝流程,銳創(chuàng)等企業(yè)能夠生產(chǎn)出高質(zhì)量的端子用銅帶,滿足客戶的不同需求。